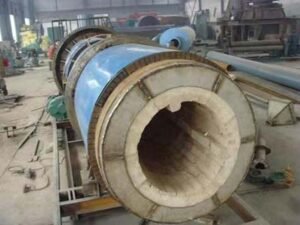
Selecting the corresponding refractory materials according to the erosion of different high-temperature gases on the kiln. Due to the different operating conditions of high-temperature kilns, the corrosive components in their combustion gases are also different, which leads to various serious erosions of the refractory materials in contact with them. This shows that only by selecting the corresponding refractory materials according to the specific conditions of use can a long service life be obtained. Specifically, there are the following:
1. In a rich furnace with high-temperature gas with high CO content, non-oxide refractory materials, especially C-SiC refractory materials, are the best choice.
2. In a rich furnace with high-temperature gas containing CI2 or/and HCI, SiO2-AI2O with the lowest FeO content as possible is selected, and the refractory materials can meet the use requirements.
3. The combustion gas of the cement rotary kiln fueled by waste oil contains a large amount of CI2 and SO, so MgO-Spinel refractory with high resistance to sulfur and chlorine erosion should be selected, especially the third-generation Mg0-Spinel (A12O3) refractory manufactured by the strengthening technology of Spinel combination. This high-performance refractory is a high-tech MgO-Spinel (A12O3) refractory characterized by fused magnesia and fused Spinel based on high-quality Spinel (in-situ Spi-nel). It can improve the resistance to liquid phase erosion caused by overheating. The use results show that this high-performance MgO-Spinel (A12O3) refractory is particularly suitable for the use conditions of waste oil as fuel with large fluctuations in combustion value, resulting in serious local erosion, and can significantly extend its life.
4. For lining refractory materials in contact with high-temperature gases containing alkalis and SO3, such as the middle section checker bricks of the glass kiln regenerator, MgO-2MgO·SiO2 refractory can be selected. Because they not only have a high ability to resist alkaline sulfate erosion, but also are cheap. When it is necessary to further improve the corrosion resistance, MgO-ZrO2·SiO2 refractory materials can be used. Because ZrO2·SiO2 in this refractory reacts with Mg0 at high temperature to form 2MgO·SiO2 and f-ZrO2 to form a 2MgO·SiO2-ZrO2 continuous matrix phase, its corrosion resistance is very strong. Since the highly corrosive CI2, HCI, SO3 and alkalis contained in the high-temperature gas in the kiln have the characteristic of high permeability, it is believed that the selected refractory must have the advantages of high density, low permeability, and good thermal shock resistance to adapt to it.