Clay bricks and high-alumina bricks are different in appearance. Clay bricks are relatively rough, while high-alumina bricks are smoother.
High-alumina bricks and clay bricks are not only different in alumina content. Their production processes are similar, but the clinker content in the ingredients is higher, and the firing temperature is much higher than that of clay bricks. In actual tests, the first and second grade high-alumina bricks are mostly used in tunnel kilns with a temperature of 1500-1600C.
High-alumina bricks are distinguished according to the amount of aluminum oxide (Al2O3) content. Currently, 48%, 55%, 60%, 65%, and 75% are commonly used. Of course, there are also corundum bricks with higher contents.
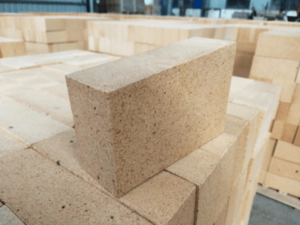
According to the amount of content, those below 48% are called clay bricks, which are a neutral refractory material made of bauxite or other materials with high alumina content and fired. It has high thermal stability and a refractory temperature of about 1700C. Refractory brick manufacturers use it for glass melting furnaces: aluminum cement rotary kilns, and steelmaking electric furnace linings. Of course, there are also some refractory bricks with high load softness and different parts of rotary kilns. How should we choose them? High-alumina clay bricks with low creep and low pores, high-alumina bricks, high-alumina bricks, finished products, according to different application needs, the ratio of raw materials in production is very important. Clay bricks are refractory bricks made of refractory clay and its clinker through processes such as crushing, mixing, molding, drying and acetylene feeding. Clay bricks are divided into three grades according to physical and chemical indicators, namely (NZ)-40, (NZ)-35, and (Nz)-30. Their main properties and suitable humidity ranges are listed in the appendix. (NZ)-40 clay bricks are the main material for building the high temperature section of the heating furnace, (Nz)-35 clay bricks are commonly used for building the low temperature section of the heating furnace, and (Nz)-3D clay bricks are used for building the flue.
High alumina bricks use high alumina as the main raw material, with soft raw clay as a binder, and are fired at a high temperature of about 1500℃ after molding. High alumina bricks contain more than 48% Al2O3. Its refractoriness, load softening point and reburning shrinkage are higher than clay bricks, but its resistance to rapid cooling and heating is worse than clay bricks. High alumina bricks are neutral refractory materials, and their slag resistance increases with the increase of Al2O3 content. There are three grades of ordinary high alumina bricks, namely (Lz)-65, (Lz)-55, and (Lz)-75.
High alumina bricks are mainly used for lining blast furnaces, hot blast furnaces, electric furnace roofs, blast furnaces, reverberatory furnaces, and rotary kiln linings. In addition, high alumina refractory bricks are also widely used as flat furnace regenerative checker bricks, plugs for pouring systems, nozzle bricks, etc. However, the price of high alumina bricks is higher than that of clay bricks. Generally, when using them, it is determined by the normal temperature of the kiln. Which refractory brick is suitable? If clay bricks can meet customer requirements, it is recommended that customers use refractory bricks of the appropriate grade.
High alumina bricks are a neutral refractory material with an aluminum oxide content of more than 48%. They are formed and calcined from bauxite or other raw materials with a high aluminum oxide content. They have high thermal stability and a refractoriness of more than 1770℃. They have good slag resistance. They are used for lining steelmaking electric furnaces, glass melting furnaces, cement rotary furnaces, etc. Refractoriness, the refractoriness of high alumina bricks is higher than that of clay bricks and semi-silica bricks, reaching 1750-1790℃, and are high-performance refractory materials.
Load softening temperature, because high-alumina products have high Al2O3 , less impurities, and less fusible glass, so the load softening temperature is higher than that of clay bricks, but high-load softening, low creep high-alumina bricks are high-performance refractory materials made of special bauxite, fused corundum, and fused mullite as the main raw materials. This product has the advantages of small high-temperature creep, strong corrosion resistance, and good thermal shock stability. It is suitable for large and medium-sized hot blast furnaces. It opens up the next successful path for the localization of high-quality, second-imported refractory materials required for new hot blast furnaces in my country. Because mullite crystals do not form a network structure, the load softening temperature is still not as high as that of silica bricks. Slag resistance, high-alumina bricks have more Al2O3, which is close to neutral refractory materials, and can resist the erosion of acidic slag and alkaline slag. Because it contains SiO2 , its ability to resist alkaline slag is weaker than its ability to resist acidic slag.
High alumina bricks are based on clay bricks, but with a changed AI2O3/SiO2 ratio and increased AI2O3 content. Therefore, the refractoriness and high-temperature mechanical strength are better than clay bricks, and the chemical properties are also neutral. It can be considered that all parts of thermal equipment that originally used clay bricks can be replaced by high alumina bricks, and silica bricks can also be replaced in some parts. Blast furnaces, hot blast furnaces, electric furnace tops, steel plugs, cement kilns, glass kilns and chemical industry kilns use high alumina bricks to increase the operating temperature and extend the service life. Therefore, high alumina bricks have been widely used in various thermal equipment. After high alumina plugs and nozzle bricks replaced clay plugs and nozzle bricks, the leakage of steel that often occurs when pouring boiling steel was overcome.
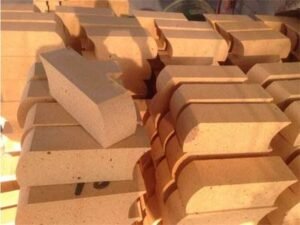