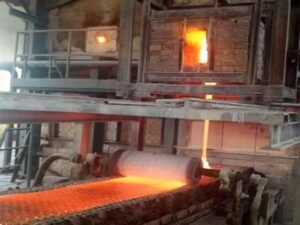
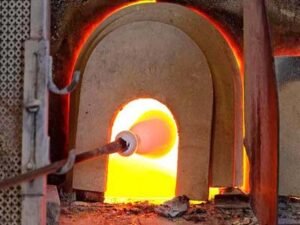
Basic principles of kiln maintenance and management
(1) During the kiln construction period, supervision and follow-up of the construction progress is an important task of kiln maintenance; before the kiln is put into use, some emergency hot-repair refractory materials should be prepared, such as high-alumina bricks, zirconium mullite bricks, zero-expansion silica bricks, sealing ramming materials, etc.
(2) After the kiln is baked, the kiln should be sealed carefully, which will directly affect the subsequent operation status of the kiln;
(3) During the operation of the kiln, if some minor problems occur at ordinary times, they should also be handled in time; if cracks or cracks occur, they should be sealed immediately to ensure that the furnace is in good condition.
(4) After six months of operation, the heat storage body of the heat storage chamber should be carefully inspected and cleaned. For the three-channel heat storage chamber, a planned inspection and treatment should be made three months after it is put into operation. The inspection frequency is usually low in the early stage, and the number of inspections will gradually increase with the increase of years of use.
(5) For the arch top and furnace wall, it is not recommended to simply apply or “cover” the seal after the fire is passed, but to thoroughly “remove the mud” and then seal from the “root”.
(6) To control the flame of the kiln well, you must be able to “watch the fire” and do it regularly.
(7) The refractory material must have a refractoriness above the temperature of the daily operation of the kiln, and it must not be at the critical temperature it can withstand, which will seriously affect the service life of the kiln.
(8) Carry out kiln operation management work in accordance with “zero pressure” or “micro-positive pressure” and reasonably manage and control the furnace pressure.
Regular inspection and maintenance
(1) Dust removal in the heat storage chamber: Routine inspections should be carried out for new kilns after six months of operation, and dust removal should be carried out in time. This includes checking and cleaning the blockage of the heat storage body cylinder bricks or checker bricks, and dust removal at the bottom of the heat storage chamber. Even if there is no blockage, careful inspection and dust removal operations should be carried out. For three-channel heat storage chambers, troubleshooting and dust removal should be carried out after three months of operation.
(2) Thoroughly handle minor problems: Minor problems that occur in the kiln on a daily basis should be handled immediately to reduce or avoid the possibility of other failures or accidents. The repaired parts and the surrounding area should be cleaned and sealed.
Safety inspection and improvement management
The kiln should have a corresponding inspection system at different times, distinguishing key inspection parts (for example: liquid flow holes, corners of the feeding port, etc.), and judgment of the operating status (for example: kiln pressure at the glass liquid level, cooling air conditions, etc.). The inspection should be careful and serious, and should not be “formalistic” and perfunctory. Records should be kept for daily inspections to prepare for the analysis of the causes of kiln failures and the judgment of kiln change trends, and to prepare for scientific and reasonable planning.