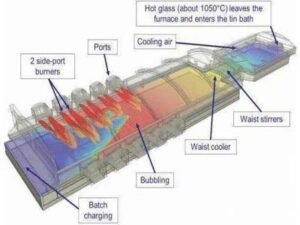
Glass electric melting furnace baking requirements
(1) Electrode: For electric melting furnaces equipped with tin oxide electrodes, due to the poor thermal shock resistance of tin oxide electrodes, it is necessary to maintain an oxidizing atmosphere before the electrodes are immersed in the ignition furnace glass, and the oxygen content is too high or the temperature fluctuates.
(2) Refractory materials: The thermal expansion of refractory materials and their sensitivity to temperature are directly related to the formation of the heating curve.
(3) Kiln structure: When the kiln body is baked, the main burner heats and burns in the upper space. Due to the structural characteristics of the electric melting furnace, it is required to maintain a high positive pressure in the furnace so that the exhaust gas is discharged from the upper part of the electric melting furnace to the lower part of the electric melting furnace through the ascending channel and the material channel, so that the temperature of these components is synchronized with the ascending space of the electric furnace. When the liquid hole is sealed by molten glass, the small burner at the top of the ascending channel heats the riser and the feed channel, which requires a high positive pressure.
(4) Burner and fuel: The burner should be easy to adjust, the flame formed should be short and bright, the combustion should be better when there is no flame, it can work normally under high positive pressure, and the temperature rise can be carried out smoothly as required. The fuel should have a high calorific value and burn stably. It is best to use gas fuel throughout the kiln process.
Electric furnace baking kiln process
The baking process of the electric furnace is also the heating process of the electric furnace. In order to make the heating process go smoothly, the heating curve must match the size, structure and refractory materials used. The heating process should save time and energy as much as possible, while avoiding damage caused by the heating process.
The baking kiln of the electric furnace is divided into two stages. The first stage is the drying stage of the refractory material, using gas as fuel. In order to bake all parts of the kiln, the chimney damper should be closed to generate positive pressure in the kiln system. This stage lasts about two days. The temperature of the upper structure of the kiln body is the highest, the control flame is sky blue, and the oxygen measuring device is not installed. The second stage is the main heating stage of the electric furnace. Under the premise of following the requirements of the baking furnace, the main body of the electric furnace is heated according to the heating curve and the temperature is increased as much as possible. The electric furnace needs to be kept at a suitable temperature in order to allow the liquid hole, the rising channel and the feeding channel to have more heating time before the electric furnace is fed.
Common problems and solutions during the kiln drying process
(1) The temperature rise of the material channel and the rising channel is slow. Part of the heat comes from the upper radiation heat, and the other part of the heat is taken away by the exhaust gas generated through the rising channel and the material channel. Since the flue gas rises due to the heat, it is difficult to discharge from the molten pool into the clarifier as expected, and it is also difficult to discharge through the liquid hole, the rising channel and the feeding channel.
The kiln pressure in the kiln flame space can be appropriately increased, some holes and gaps can be blocked, and the exhaust gas loss can be reduced. A high temporary chimney is added at the end of the channel, and a pipe is inserted from the bottom to the top at the bottom of the chimney. The gas in the channel is blown upward to absorb the gas, reduce the pressure in the channel, and increase the upper space of the furnace. The pressure difference between the channels increases the amount of exhaust gas entering the channel, and the temperature rise of the liquid hole, the rising channel and the channel part is significantly increased.
(2) Insufficient oxygen. The electric melting furnace equipped with tin oxide electrodes measures the oxygen content through the observation hole on the kiln wall, takes measures to improve the mixing degree of fuel and air, and uses a secondary atomizing burner for combustion. Above the burner, force explosion at a certain angle to make the fuel burn fully, reduce the amount of liquid fuel, increase the gas burner and explosion point, thereby accelerating the combustion of liquid fuel and exceeding the excess oxygen! ”
(3) Cracks in the brick joints. During the heating process, the temperature sometimes fluctuates up and down. If the expansion bolts are loose, the fused zirconia corundum bricks are not firmly bonded and there are brick joints. There are also several cracks in the upper space. After the hot broken glass, there are multiple leaks (especially in the corners of the melting pool). Use a fan to blow air at the leak to freeze the glass liquid. Strengthen the top screw to minimize the gap between the electric melting brick and the backing brick.
(4) Cracks in the furnace door. When the furnace door of the kiln is cracked or damaged, temporary refractory bricks should be built, and a feeding door should be left in the middle. After bricklaying, the outer layer is reinforced with asbestos board. After the kiln is completed, carefully remove the ceramic fiberboard.
(5) The compressed air has a large water content and the combustion is discontinuous. If the compressed air used for atomization has a large water content, resulting in intermittent combustion, and the oxygen content in the compressed air is low, a section of the pipe can be removed from each pipe branch and two pipe branches can be installed. Install an oil-water separator and use the two pipe branches alternately, which greatly reduces the water content in the compressed air.