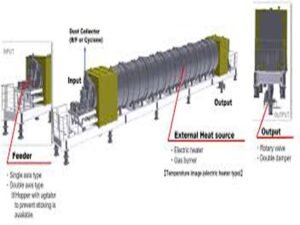
During the operation of cement rotary kilns, refractory materials in the kiln are frequently subjected to thermal, chemical and mechanical stresses, which can cause different forms of damage.
The consensus reached through the operation practice of cement kilns is that mechanical stress, thermal stress and chemical erosion are the three most basic damage factors. In most cases, they act on refractory materials in combination, and are mainly manifested as thermal-mechanical and thermal-chemical effects. A large number of studies have been conducted on used magnesia-chrome bricks, and the frequency of the main causes of damage has been counted:
1)Mechanical stress accounts for 37%: caused by kiln body deformation and thermal expansion of bricks.
2)Chemical erosion accounts for 36%: caused by the erosion of silicates, ferrites and alkali salts in clinker.
3)Thermal stress accounts for 27%: caused by overheating and thermal shock.
The use of PC kilns and SP kilns, due to the high working temperature in the kiln, the fast kiln speed, the complex mechanical structure, and the enrichment of alkali volatile components, the kiln lining is severely alkali-corroded, resulting in a significant shortening of the service life of the refractory materials. The damage mechanism of the kiln lining materials is as follows:
1.Severe erosion by volatile components such as alkali, sulfur, and chlorine
Since the pre-decomposition kiln fully utilizes the waste heat to preheat the raw materials, sulfates and chlorides are volatile and condensed, repeatedly circulated and enriched, resulting in severe erosion of refractory materials such as clay bricks and ordinary high-alumina bricks used in preheaters, decomposition furnaces, ascending flues, and unloading slopes, forming new minerals that expand, causing the refractory materials to crack and peel off, and “alkali cracking” damage occurs. In addition, volatile components such as sulfur and chlorine form crusting minerals such as 2C2S·CaCO3, 2C2S·CaSO4, and 2CaSO4·K2SO4 on the surface of the refractory materials they contact, aggravating the structural peeling and damage, seriously interfering with the normal operation of the kiln, and even stopping the kiln for maintenance.
2.Increased kiln temperature intensifies damage to refractory materials
Large pre-decomposition kilns mostly use grate coolers and multi-channel coal nozzles. The secondary air temperature can reach 1150℃, and the flame temperature is much higher, causing the temperature level of each section to be much higher than the corresponding parts of traditional kilns. The increase in temperature intensifies the erosion of clinker on refractory materials, and the service life drops sharply.
3.Increased kiln speed and kiln diameter increase the thermal mechanical damage to the kiln lining
The speed of large kilns reaches 3~4r/min, the diameter is as high as 4~6m, the unit output increases, but the kiln skin becomes worse, the thermal shock damage is large, and the mechanical stress and thermal fatigue damage are also increased.
In addition, in recent years, cement kilns have continuously used various industrial wastes, such as waste tires, as auxiliary fuels, making the erosion of alkali, chlorine, and sulfur increasingly serious. The magnesium spinel bricks that used to work well in the transition zone have significantly reduced their lifespan with the continuous increase in the amount of industrial waste.
Among them, the firing zone and transition zone of the cement rotary kiln are the parts with the worst working environment in the whole system. They are subjected to more wear than other sections and are affected by the comprehensive thermo-mechanical and thermo-chemical effects. 60%~70% of the total consumption of refractory materials in the whole kiln system occurs in the firing zone and transition zone.
In addition, the metal shell of the kiln is not completely rigid. Coupled with the influence of the excessive ellipticity of the kiln, the kiln body, especially the wheel belt, undergoes deformation to a greater or lesser extent during the rotation of the kiln, resulting in compression, tension and shear stress in the kiln lining. In addition, the continuous relative displacement and local stress between the refractory materials lead to cracking, peeling and even shearing of the material.